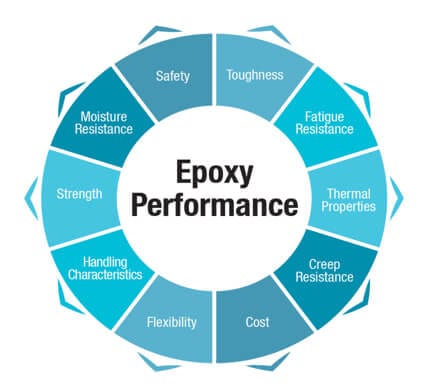
WEST SYSTEM marine epoxy has been continually formulated, tested and improved for 50 years to produce the most reliable and well-balanced marine epoxy system available.
Potential marine epoxy resin and hardener formulas, ingredients and combinations are tested to compare fatigue strength, compression strength, glass transition temperature, and peak exotherm. Qualified samples are tested for hardness, tensile strength, tensile elongation, tensile modulus, flexural strength, flexural modulus, heat deflection temperature, impact resistance and moisture exclusion effectiveness.
Thorough testing such as this insures that any change in a formula will improve one or more of the product’s characteristics without diminishing any characteristics.
Fatigue aspects of epoxies and epoxy/wood composites
In materials science, fatigue is the name for the process of weakening materials and structures by subjecting them to repeated loads. This paper addresses the cyclic fatigue-related degradation of epoxy composite materials and serves as a guide to a better understanding of this very complex composite material failure mode.
Moisture Exclusion Effectiveness
WEST SYSTEM epoxy is often used to provide a moisture barrier for applications that are in frequent or constant contact with water. In order to gain a more complete understanding of the moisture resistance properties of WEST SYSTEM, Gougeon Brothers Inc use accelerated testing to measure the ability of a coating applied in a relatively thin film to resist water transmission.
This test is call Moisture Exclusion Effectiveness ( MEE), based on a method developed by the USDA Forest Products Laboratory.
The Moisture Exclusion Effectiveness Test
The MEE test begins with Douglas fir plywood blanks with corners and edges sanded round. A small cup hook is installed in each end. The sample blanks are then conditioned in the Arizona room, a hot/dry room kept at 38oC with a relative humidity close to 0%, for 2 weeks or until the moisture content of the blanks levels out close to 0%.
The blanks are then removed from the hut, allowed to assume room temperature, and weighed very accurately to 4 decimal places. This is recorded as the dry weight.
Next, the blanks are coated with whatever product is being tested – WEST SYSTEM and also competitors including other epoxies, paints, polyesters, vinylesters, etc. Generally 5 samples of each are made with 1, 2 and 3 coats for a total of 15 pieces for each test material. Five samples generate an acceptable average, and the increasingly thicker coating allows for a curve to be generated for each test material.
After the coatings are completely cured, the weight is recorded again. Samples are then hung in a rack and placed in the Florida room, a hot/wet hut that is kept at 38o C and 100% relative humidity. The weight gain is measured each week for 6 weeks or until the test curves begin to flatten out. As with any good test procedure, control samples left uncoated, are run alongside the test samples.
Because all coatings are semi-permeable membranes, GBI can generate curves that compare the relative permeability of various coatings. As shown in chart below, WEST SYSTEM R105/H205 performs well relative to the other materials tested, provides a superior moisture barrier, combined with excellent mechanical properties.
Creep Rupture
Creep stress is a material property that describes how a material resists the stress of a constant long-term load.
Creep stress problems can be evident when something simply does not hold its shape.
Creep stress can also result in a complete failure, such as when a highly stressed glue joint at the stem of a boat fails months after the glue has fully cured when the boat is moored at the dock. In these cases, it can be said that the material has flowed or “crept” due to constant stress.
WEST SYSTEM 105 is formulated to be resistant to creep-stress and Gougeon Brothers, Inc have developed a large database of creep stress performance of WEST SYSTEM epoxy, competitive epoxies and popular urethanes.