Cold Weather Bonding
“What’s the lowest temperature WEST SYSTEM Epoxy can be applied?” By Don Gutzmer WEST SYSTEM Inc, USA
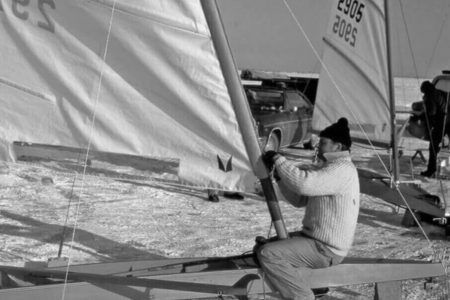
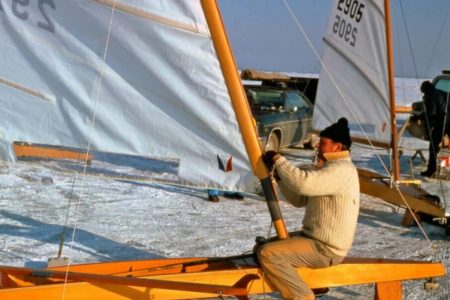
During cold weather, this is a common question our Technical Advisors are asked. Fortunately, it’s one we’re well equipped to answer. Gougeon Brothers, Inc. got its start in the world of DN Iceboat racing. Both Meade and Jan Gougeon have won multiple DN cup races worldwide. It’s not unusual for an iceboat to need repairs mid-regatta, so part of the discipline of iceboat racing is getting epoxy to cure despite cold working environments. The trick is using strategies that bring epoxy temperatures up to adequate cure levels in cold working environments.
The ambient temperature in which an epoxy chemical reaction takes place impacts on the rate of the reaction. Warmer temperatures accelerate the reaction, while cooler temperatures retard the reaction time. It is the duration of the reaction which, among other variables, will lead to complete or incomplete bonding of the epoxy molecules. Improperly cured epoxy may possess enough strength to hold the structure together, yet it may fail after being subjected to repeated loading during normal operations.
Step
1
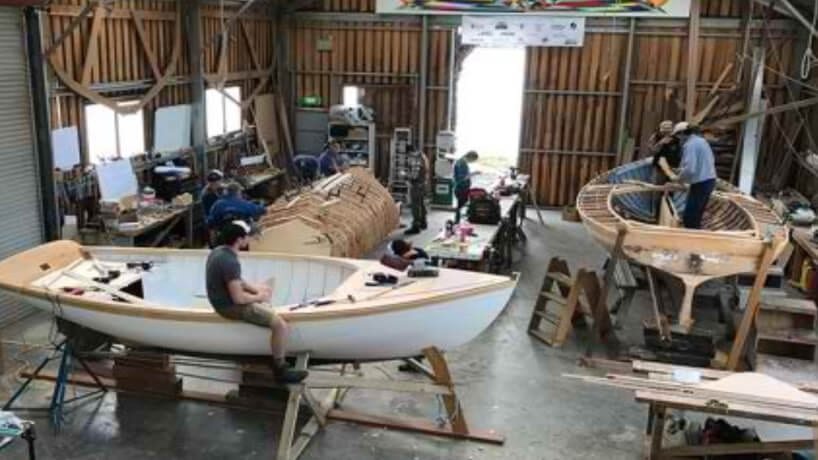
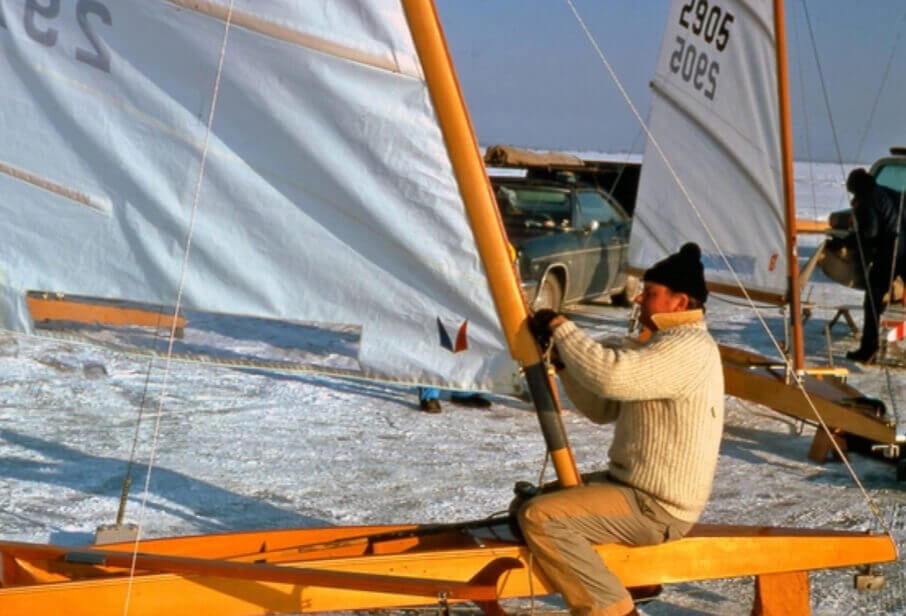
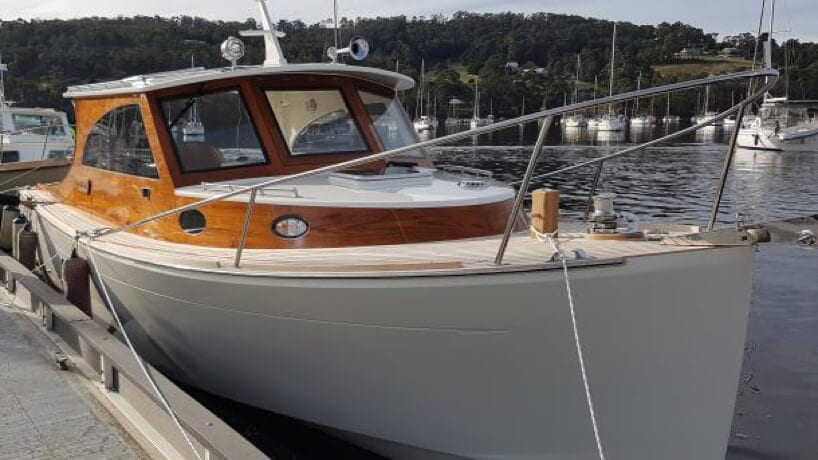
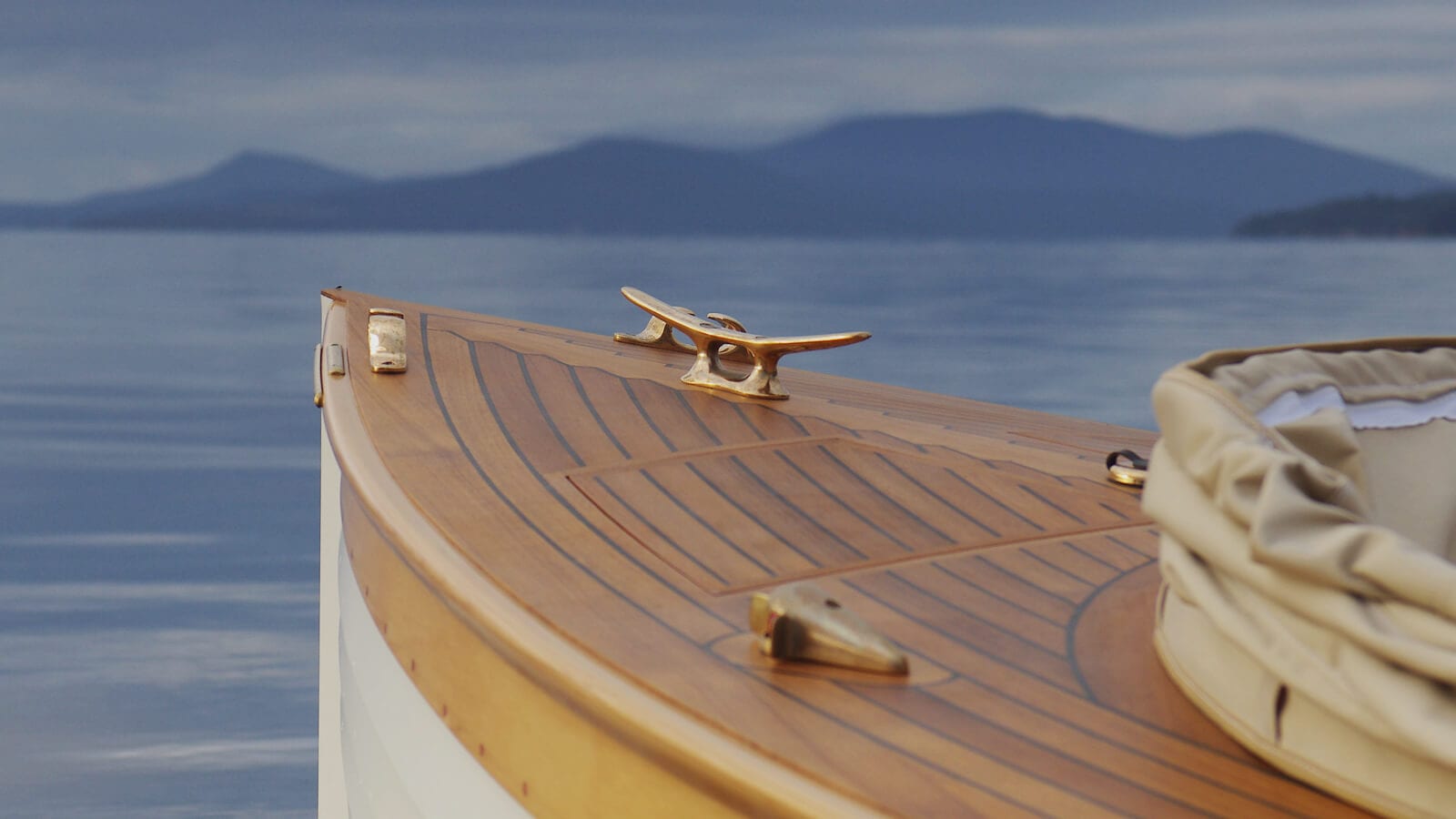
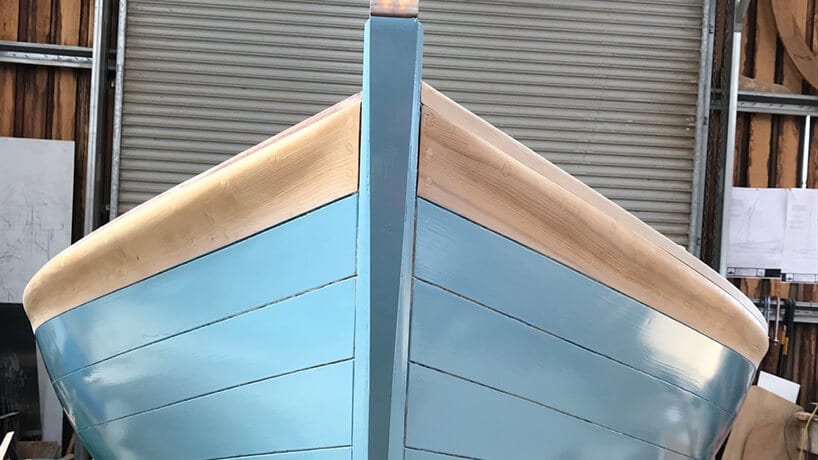
Use WEST SYSTEM 105 Resin and 205 Fast Hardener. 205 Fast Hardener is formulated to cure at temperatures as low as 4°C, but this does require an extended cure time before removing clamps or sanding. 206 Slow Hardener and 207 Special Clear Hardener should not be used below 16°C unless you elevate the working temperature to allow the system to cure properly.
For best results when clear coating with 207 Hardener, postpone coating until the temperature in your working environment is around 21°C. 209 Extra Slow Hardener should not be used below 21°C.
Step
2
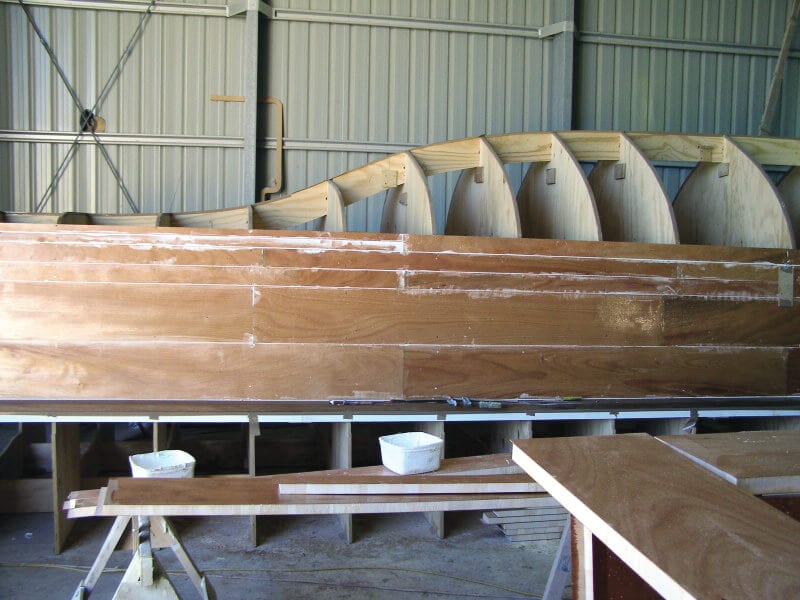
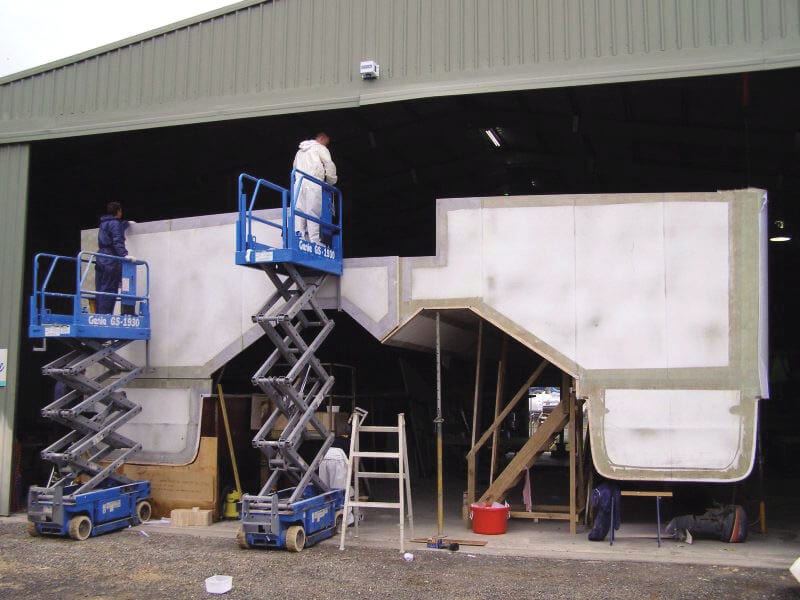
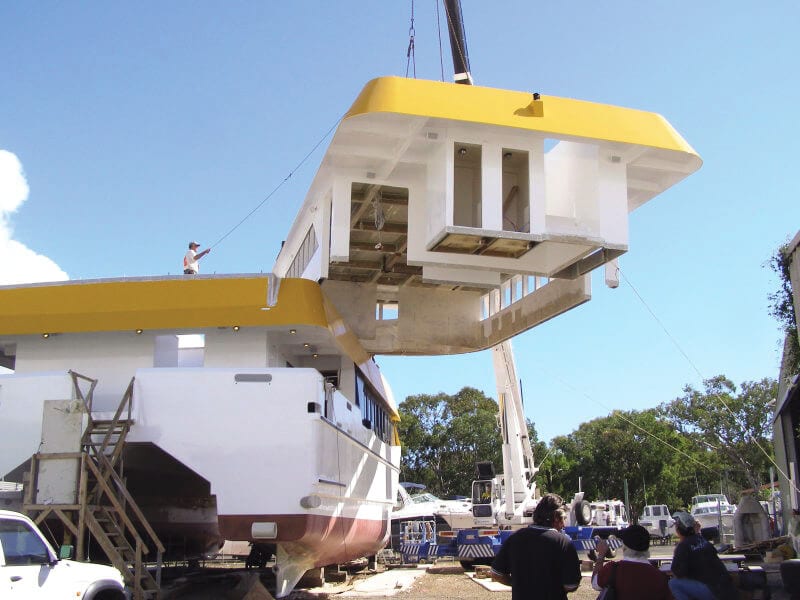
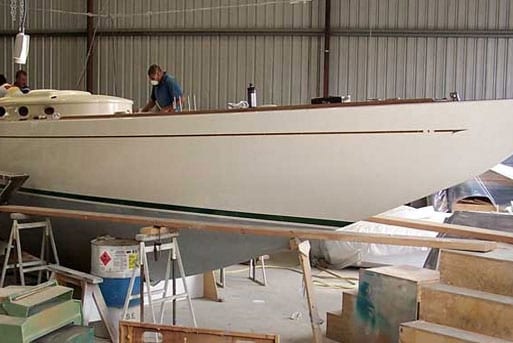
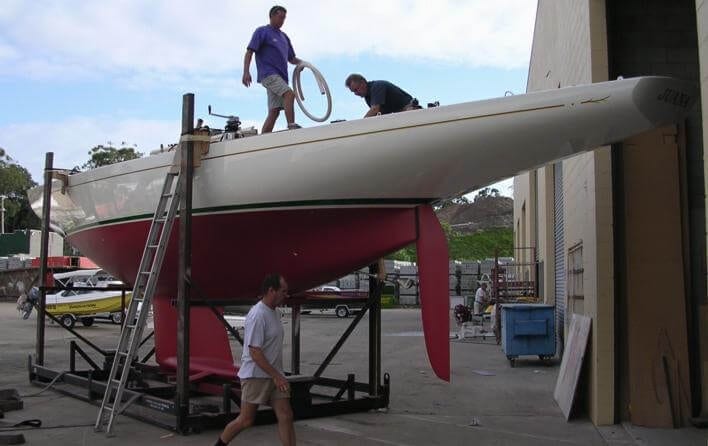
Warm resin and hardener before using. Cold temperatures increase the viscosity of the epoxy, making it more difficult to dispense, mix and apply. Warming the resin and hardener lowers their viscosity, allowing the product to flow through the dispensing pumps better, cling less to the containers and mixing equipment, and blend more easily for thorough mixing. The warmer, lower-viscosity mixture will flow more smoothly during application and penetrate porous surfaces more efficiently.
Methods for warming resin and hardener before use:
- Leave the containers in a warm area.
- Place a heat lamp near the containers.
- Put containers in a cooler with a light bulb or heating pad.
- Build a custom warming box out of rigid sheets of foil-backed insulation and keep it warm with a lightbulb or heating pad.
In any case, you will want the resin and hardener at a temperature between 21°C to 32°C. These methods keep the warmed resin and hardener close to your work and allow less time to cool off between dispensing and application. Warming the epoxy helps the initial chemical reaction get off to a better start, and results in more cross-linking even if the mixture cools when it is applied to a cold substrate.
Step
3
Step
4
Step
5
Step
6
Step
7
Step
8
Cold Weather Storage
Remove from the water, replace the lids tightly and invert the container to melt any crystals which may be clinging to the top of the container. If the resin has crystallized inside the mini pump, pumping warm resin through it should dissolve them. Leaving the pump in the can while heating should clear the pump, too. With a little advanced planning, and observing the precautions listed above, you can get WEST SYSTEM Epoxy to cure reliably in cold working conditions. Since the 1970s we’ve been using these techniques to assure dependable epoxy bonds throughout our frigid Michigan winters.
When using WEST SYSTEM epoxy at low temperatures, special precautions can be taken to assure maximum performance.